Maximizing Efficiency and Innovation in Construction and Manufacturing with the Cement Silo
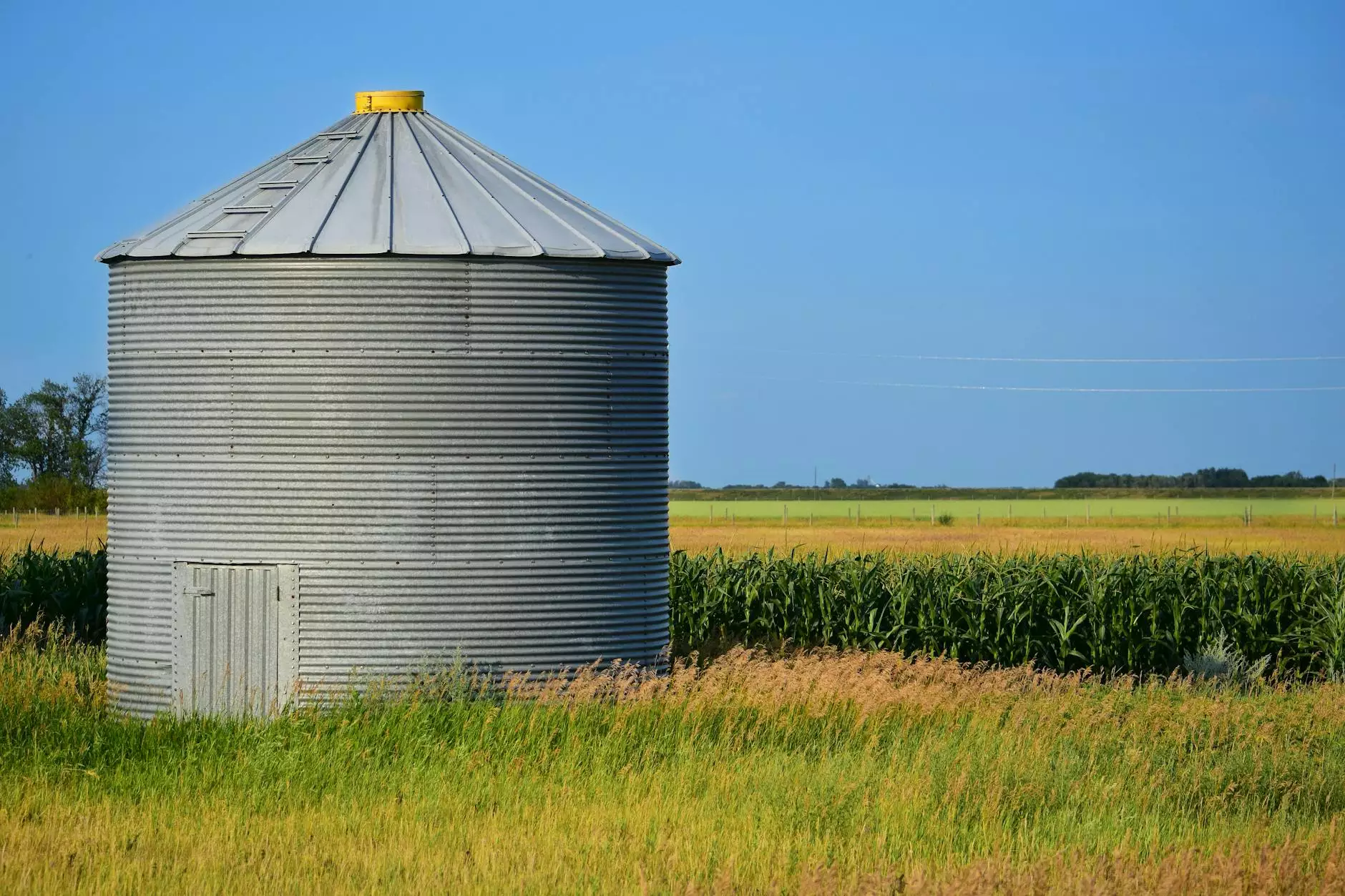
In the rapidly evolving world of construction and manufacturing, the integration of advanced equipment is vital for ensuring productivity, safety, and cost-effectiveness. Among these technological innovations, the cement silo stands out as a cornerstone component that significantly enhances silo operations, material handling, and overall project efficiency. This comprehensive guide explores the multifaceted benefits, innovative designs, and strategic applications of the cement silo in modern industries, aiming to inform executives, engineers, and project managers about maximizing their operational potential.
What Is a Cement Silo and Why Is It Essential in Modern Industries?
A cement silo is a specialized storage unit designed to hold bulk quantities of powdered materials such as cement, fly ash, or other fine aggregates used in concrete production and construction projects. Its primary purpose is to facilitate a seamless flow of materials directly into mixing plants, reducing manual handling and minimizing contamination risks. This equipment is vital in maintaining the quality, consistency, and timely supply of materials, especially for large-scale projects.
The importance of a cement silo extends beyond mere storage; it embodies efficiency, safety, and innovation. Its capacity ranges from small portable models to massive fixed structures capable of storing thousands of tons of cement, making it adaptable to diverse project sizes and industrial needs.
Key Types of Cement Silos: Tailoring Storage Solutions to Industry Needs
Industry professionals have developed various types of cement silos tailored to specific operational requirements:
- Steel Cement Silos: Known for durability and strength, steel silos are ideal for long-term storage and are resistant to harsh environmental conditions.
- Concrete Cement Silos: Built with reinforced concrete, these are favored for their robustness and ability to withstand heavy loads, suitable for large-scale industrial applications.
- Portable Cement Silos: Designed for flexibility, these small, mobile units are perfect for remote or temporary projects, allowing quick deployment and easy relocation.
- Bolted vs. Welded Silos: Bolted silos facilitate easier assembly and disassembly, proving advantageous for temporary operations, while welded silos offer superior structural integrity for permanent installations.
Innovative Features of Modern Cement Silos
Cutting-edge cement silos incorporate several technological advancements:
- Automation and Sensor Technology: Integrated sensors monitor fill levels, temperature, and pressure, enabling automated alerts and optimizing material flow.
- Dust Collection Systems: Modern silos are equipped with advanced filtration systems that minimize dust emissions, promoting environmental sustainability and worker safety.
- Easy Maintenance Design: Access points, cleaning hatches, and modular components simplify routine maintenance, increasing operational uptime.
- Energy-Efficient Operation: Variable speed drives and energy-efficient motors reduce operational costs and environmental impact.
Benefits of Integrating a Cement Silo Into Your Construction & Manufacturing Processes
The strategic adoption of cement silos yields numerous advantages that directly impact project success:
- Enhanced Material Handling and Storage Efficiency: Large capacity and quick loading/unloading streamline supply chains within the construction site or manufacturing plant.
- Improved Quality Control: Contained storage minimizes moisture ingress and contamination, ensuring cement and other powders retain optimal properties.
- Cost Savings: Bulk storage reduces procurement frequency and handling costs, while minimized waste lowers overall expenses.
- Time Optimization: Continuous supply capabilities eliminate delays in production schedules, facilitating faster project completion.
- Environmental Compliance and Safety: Dust collection and sealed systems decrease environmental impact and improve site safety standards.
Strategic Considerations When Choosing a Cement Silo
To maximize ROI, selecting the appropriate cement silo involves assessing several factors:
- Capacity Requirements: Evaluate the volume of materials needed for your project timeline to select a silo with suitable storage capacity.
- Site Conditions: Consider environmental factors, available space, and ease of access for installation and maintenance.
- Material Compatibility: Ensure the silo design accommodates the specific powders or materials used, including considerations for flow characteristics.
- Structural Durability: Opt for high-quality materials that withstand local weather conditions and long-term wear.
- Integration with Existing Systems: Compatibility with batching plants, conveyors, and automation systems is critical for seamless operations.
Innovations in Cement Silo Design for Future Industries
As industries evolve, cement silo technology continues to advance, incorporating innovations such as:
- Smart Connectivity: IoT-enabled silos facilitate remote monitoring and predictive maintenance, reducing downtime and repair costs.
- Modular Construction: Prefabricated silo modules allow rapid assembly and customization for varied project scopes.
- Sustainability Focus: Designs emphasizing energy efficiency and recyclable materials support green building initiatives.
- Hybrid Storage Solutions: Combining traditional silos with supplementary storage (e.g., mobile bins) provides flexible logistics management.
Case Studies: How Polygonmach Innovates with Cement Silos
Leading industry players such as polygonmach.com are pioneering in offering high-quality, innovative cement silos tailored to various operational needs. Their solutions showcase:
- Custom Design Capabilities: Ability to customize silo dimensions, materials, and automation features for specific client requirements.
- Integration with Electronics and 3D Printing Technologies: Incorporation of sensors and automation controls enhanced by precision 3D printed components. This synergy fosters superior performance and durability.
- Global Service Support: Extensive after-sales service and continuous innovation ensure clients remain at the forefront of industry standards.
The Future of Cement Storage: Bridging Construction and Industry 4.0
The future of cement silo technology lies at the intersection of Industry 4.0 principles. Smart silos with interconnected sensors, AI-driven analytics, and automated maintenance are transforming traditional storage solutions into intelligent hubs that optimize entire supply chains and manufacturing workflows. As digital transformation accelerates, the integration of electronics and advanced manufacturing techniques such as 3D printing will further customize and streamline silo design, installation, and maintenance.
Conclusion: Embracing Innovation for Competitive Advantage
Investing in state-of-the-art cement silos is a strategic move for businesses seeking to elevate their construction and manufacturing operations. These structures do not merely store materials; they are catalysts for operational excellence, safety, and environmental sustainability. With ongoing advances in electronics, automation, and 3D printing, companies can expect to deploy highly efficient, customizable, and smart storage solutions that drive competitive advantage in a crowded marketplace.
Whether your project demands portable silos for remote sites or massive fixed structures for large-scale factories, choosing the right cement silo with innovative features ensures your material handling infrastructure is prepared for current challenges and future growth.
Get Started with Polygonmach for Cutting-Edge Cement Storage Solutions
As a leader in industrial equipment manufacturing, polygonmach.com provides comprehensive solutions that blend traditional engineering excellence with the latest technological innovations. Explore their range of cement silos, tailored to elevate your construction and manufacturing operations today.