The Rise of China CNC Lathe Part Manufacturers
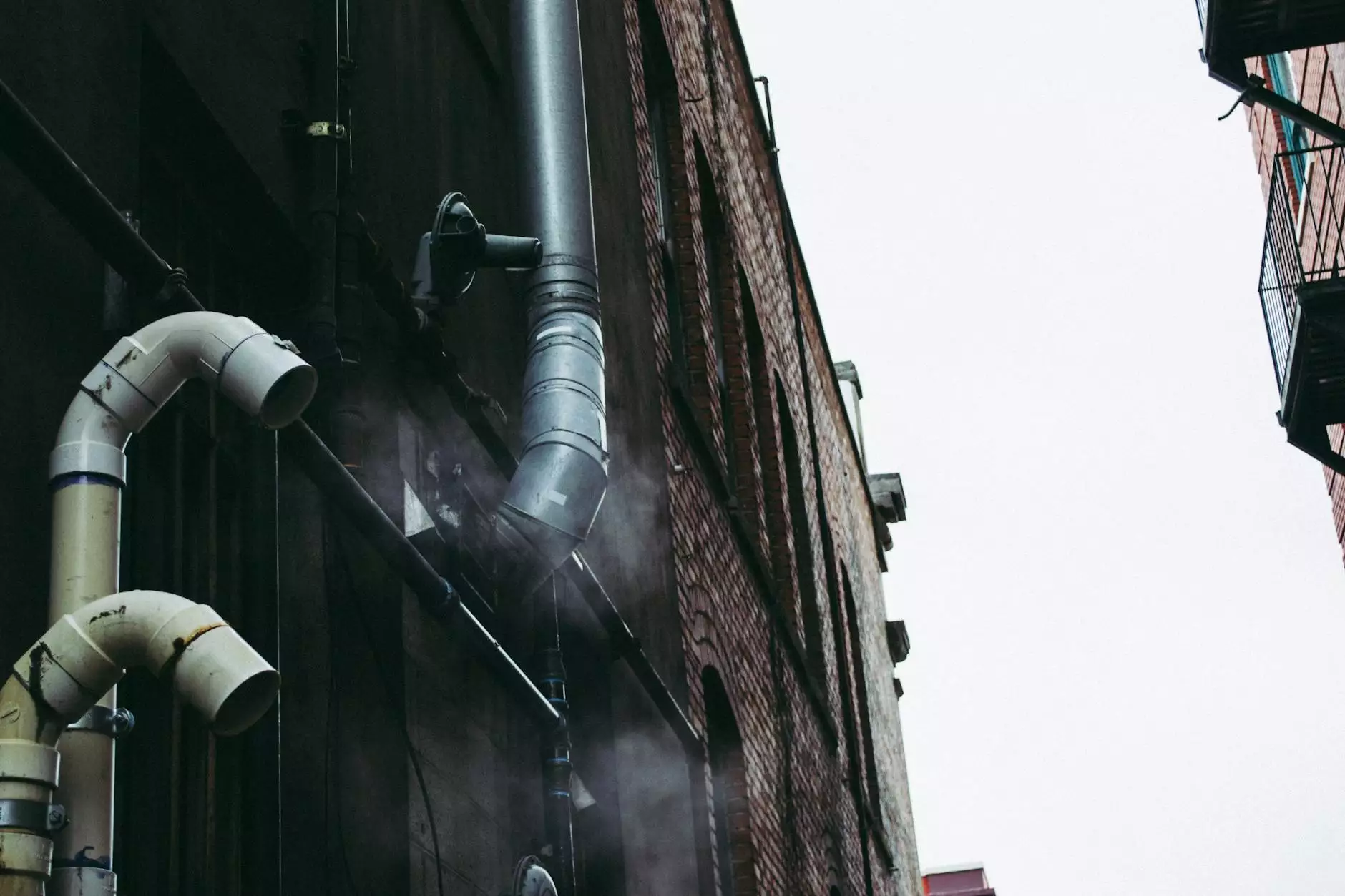
The transition in global manufacturing has been nothing short of revolutionary. Among the key players in this evolving landscape are the China CNC lathe part manufacturers. With their emphasis on quality, precision, and scalability, they have successfully carved out a significant niche within the industry of metal fabricators. In this article, we explore the intricate details surrounding these manufacturers, their processes, and their impact on the global market.
Understanding CNC Machining
To truly appreciate the role of China CNC lathe part manufacturers, it is essential to have a grasp of what CNC machining entails. CNC, or computer numerical control, is a method used for controlling machine tools through a computer. This technology enables manufacturers to streamline production while maintaining intricate details, a critical advantage in the competitive landscape of metal fabricators.
How CNC Machining Works
CNC machining transforms computer-aided design (CAD) drawings into machine-specific instructions. This process involves several key steps:
- Design: The first step is creating a precise design of the part in CAD software.
- Programming: Engineers convert the CAD file into G-code, a language that CNC machines can interpret.
- Machining: The machine follows the G-code to manufacture the part, ensuring high accuracy and repeatability.
- Finishing: Post-processing may be necessary to achieve the desired surface finish or meet stringent tolerances.
Why Choose China CNC Lathe Part Manufacturers?
The growth of manufacturers in China specializing in CNC lathe parts has opened up a plethora of opportunities for businesses worldwide. Here are some reasons why you might consider sourcing parts from these manufacturers:
1. Cost-Effectiveness
One of the most compelling reasons to engage China CNC lathe part manufacturers is cost-effectiveness. The operational costs in China, including labor and materials, are significantly lower than in western countries. This allows manufacturers to offer competitive pricing without sacrificing quality.
2. Advanced Technology
Chinese manufacturers have embraced cutting-edge technologies. Many of them leverage high-tech CNC machines equipped with sophisticated software that enhances precision and efficiency. This technological advancement ensures that manufacturers can produce complex parts with ease and accuracy.
3. Scalability and Capacity
Companies like Deep Mould, a leader in the metal fabrication industry, understand the importance of scalability. China CNC lathe part manufacturers can handle both small batch production and large-scale orders, catering to diverse business needs. This flexibility allows businesses to expand without the constraints of more traditional manufacturing setups.
Quality Assurance Standards
Quality is paramount in metal fabrication. China CNC lathe part manufacturers adhere to stringent quality assurance standards to ensure that the parts meet global benchmarks. This commitment is reflected in the following practices:
1. ISO Certification
Many manufacturers are ISO-certified, which demonstrates their adherence to international quality management standards. This certification guarantees that the processes in place consistently produce parts that meet customer and regulatory requirements.
2. In-House Testing
Advanced manufacturers conduct rigorous in-house testing and inspections. This includes dimensional inspections, material testing, and performance evaluations to ensure that parts not only meet specifications but also perform effectively in real-world applications.
The Role of CNC Lathe Parts in Various Industries
Parts produced by China CNC lathe part manufacturers find applications across diverse industries, showcasing their versatility and reliability. Here are a few significant sectors where these parts play a crucial role:
1. Automotive Industry
The automotive industry is one of the largest consumers of CNC lathe parts. From engine components to transmission parts, the need for precision and reliability is paramount. CNC lathe parts ensure that automotive components meet safety standards while optimizing performance.
2. Aerospace Sector
Aerospace engineers demand the utmost precision for components that are often subject to extreme environments. CNC machined components offer the necessary tolerances and durability, making them ideal for aircraft and spacecraft applications.
3. Medical Equipment Manufacturing
In the medical field, precision-engineered components are essential. CNC lathe parts used in medical devices must meet strict regulatory standards, and manufacturers in China are equipped to provide these detailed specifications and high-quality production.
Challenges Faced by China CNC Lathe Part Manufacturers
While there are numerous advantages to sourcing from China CNC lathe part manufacturers, the industry is not without its challenges. Understanding these can provide insight into the complexities of global manufacturing.
1. Quality Control Issues
Despite stringent quality standards, discrepancies can arise in production. Companies must work closely with manufacturers to establish clear quality control guidelines to mitigate risks.
2. Communication Barriers
Language and cultural differences may pose obstacles in collaboration. It is essential for businesses to ensure effective communication to avoid misunderstandings and ensure smooth operations.
3. Regulatory Compliance
Exporting parts from China requires an understanding of local and international regulations. Companies must navigate these laws to ensure compliance and avoid potential legal issues.
Future Trends in CNC Machining
The landscape of CNC machining is continually evolving. Several trends are shaping the future of manufacturing and the role of China CNC lathe part manufacturers:
1. Automation and Robotics
The use of automation, including robotic machining, is on the rise. This trend enhances production speeds and decreases the likelihood of human error, significantly improving efficiency in manufacturing processes.
2. Customization
Today’s consumers demand more customized products. CNC machining allows manufacturers to provide tailor-made solutions, addressing specific needs while reducing lead times.
3. Sustainable Practices
As sustainability becomes a focal point in manufacturing, Chinese manufacturers are exploring eco-friendly practices. This includes minimizing waste, utilizing energy-efficient machinery, and sourcing materials responsibly.
Conclusion
In conclusion, China CNC lathe part manufacturers stand at the forefront of the manufacturing revolution. Their combination of cost-effectiveness, advanced technology, and commitment to quality positions them as key players in the global market. As the future of CNC machining evolves with trends like automation, customization, and sustainability, these manufacturers are set to continue innovating and meeting the demands of various industries.
For businesses looking to partner with a reliable manufacturer, exploring the offerings of Deep Mould in the realm of metal fabricators might be a promising avenue. Their dedication to quality and customer satisfaction makes them a standout choice in the ever-competitive landscape of CNC machining and metal fabrication.